NanoWave
Mikrowellenhärtung von Isolier- und Vergussmaterialien für elektronische Baugruppen
Die Elektronik gehört nach wie vor zu den Wirtschaftszweigen mit der größten Dynamik. Innovative Elektronikprodukte sind in fast allen Lebensbereichen anzutreffen. Dazu gehören u.a. die Bereiche Kommunikation, Automobil, Energie und Medizin. Neue Anwendungsgebiete, verbunden mit immer komplexeren Beanspruchungen führen zu einer erheblichen Wachstumsrate im Bereich der Leistungselektronik und zu immer höheren Anforderungen an die Qualität und Zuverlässigkeit elektronischer Baugruppen.
Bedingt durch die E-Mobilität und die Hybrid-Technologie im PKW-Bereich steigen die Ansprüche insbesondere auch bezüglich der elektrischen Spannungsfestigkeit. Eine Erhöhung der Betriebsspannung bis 800 V und der umfangreiche Einsatz von Modulen der Leistungselektronik hat erhebliche Auswirkungen auf die Leiterplattentechnologie. Neue temperaturstabile Basismaterialien und Kupferinnenlagen bis zu einer Dicke von 400 µm sind notwendig. Auswirkungen ergeben sich dadurch auch im Bereich der eingesetzten Isolierstoffe, wie den Dickschichtfüllern, den Lötstopplacken und Schutzlacken (Conformal Coatings), da hochfrequente Spannungsanteile die Lebensdauer von Isoliersystemen reduzieren. Weitere Betriebsbeanspruchungen überlagern sich mit der Beanspruchung durch elektrische Spannungen zu einem komplexen Beanspruchungskollektiv.
Zur Härtung und Vernetzung von Beschichtungsstoffen bzw. Lacken auf der Leiterplatte werden vorzugsweise UV-Strahlung und IR-Strahlung eingesetzt. Bei der thermischen Härtung werden Trocknungsanlagen, in denen Infrarotstrahlung und Umluft kombiniert sind, verwendet. Es erfolgt eine Trocknung des Lackes von innen nach außen. Je höher die Schichtdicke, umso größer ist die Wahrscheinlichkeit der Bildung von Rissen im Lack. Bei höheren Schichtdicken ist das vollständige Trocknen des Lackes nicht mehr möglich und es verbleiben Lösemittelreste, die in Folgeprozessen verdampfen können. Das Auftragen und Aushärten des Lackes muss deshalb in mehreren Schritten erfolgen. Die empfohlene, maximale Trockenschichtdicke liegt im Bereich von 100 µm. Weitere Nachteile sind die langen Aushärtungszeiten, die hohen Temperaturgradienten und die thermische Belastung der Baugruppen.
Bei der UV-Härtung kann eine ungleichmäßige Verteilung der Strahlungsenergie zu Spannungen in den Lacken führen, da die verschiedenen Bereiche unterschiedlich stark ausgehärtet werden. Aufgrund der Schattenwirkung auf bestückten Leiterplatten erfolgt keine Vernetzung in Schattenbereichen (z. B. unter Bauelementen). Durch die Schwindung der Polymere baut sich ein innerer Spannungsgradient auf, so dass ein spannungsfreies und gleichmäßiges Aushärten bei dicken Schichten nicht möglich ist.
Um bei sehr dicken Schichten eine möglichst spannungsarme und homogene Durchhärtung des Materials erreichen zu können muss der Beschichtungsprozess, d.h. Auftragen des Materials und anschließendes Aushärten, in mehreren Schritten erfolgen, was längere Prozesszeiten und damit verbundene Mehrkosten zur Folge hat. Von großem Vorteil wäre es deshalb ein Verfahren zu finden, mit dem eine schnelle und homogene Aushärtung von Harzsystemen, auch bei Schichtdicken bis 400 µm und höher, möglich ist.
Project information
More research projects
CirProtech

METAWAVE
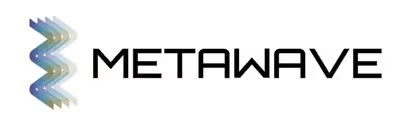
MIND
Flexby
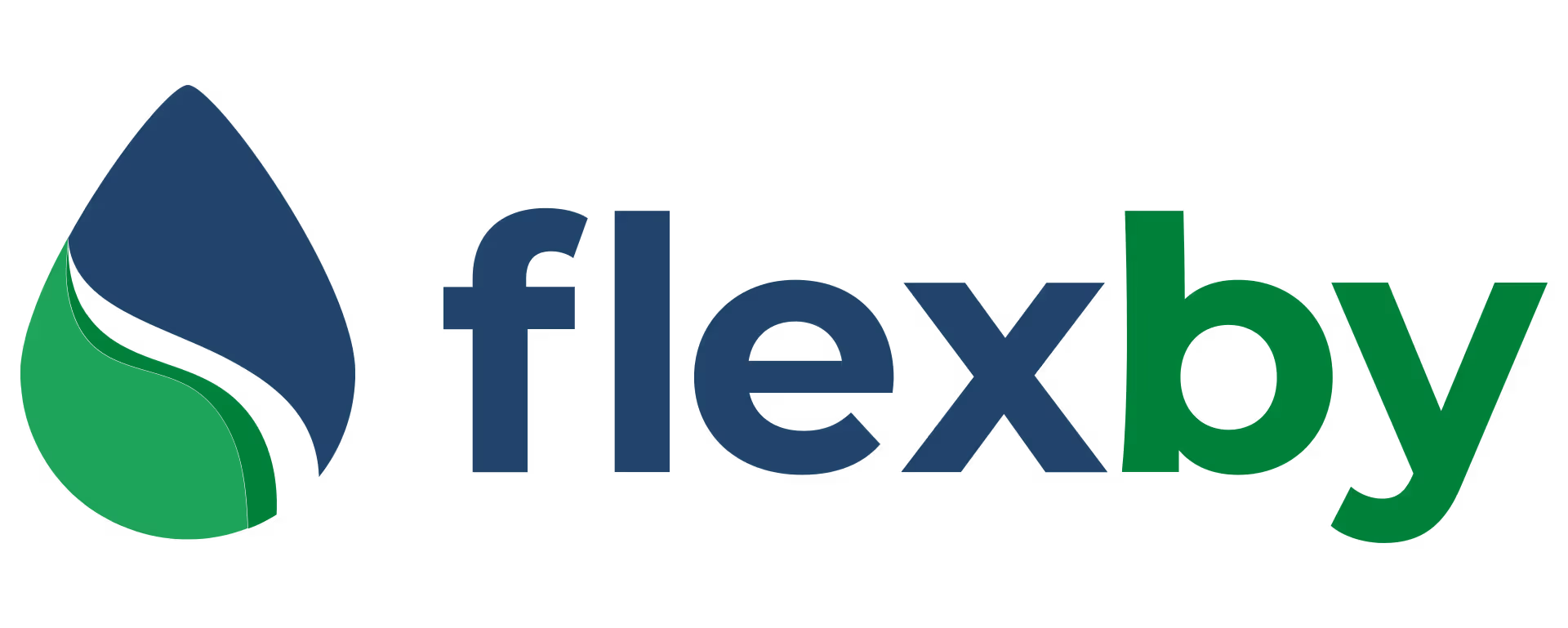
Hybrid-FIRE
CITADEL
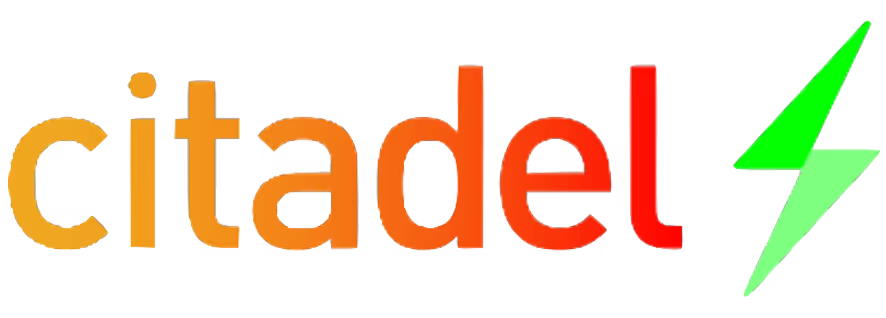
RE_SORT
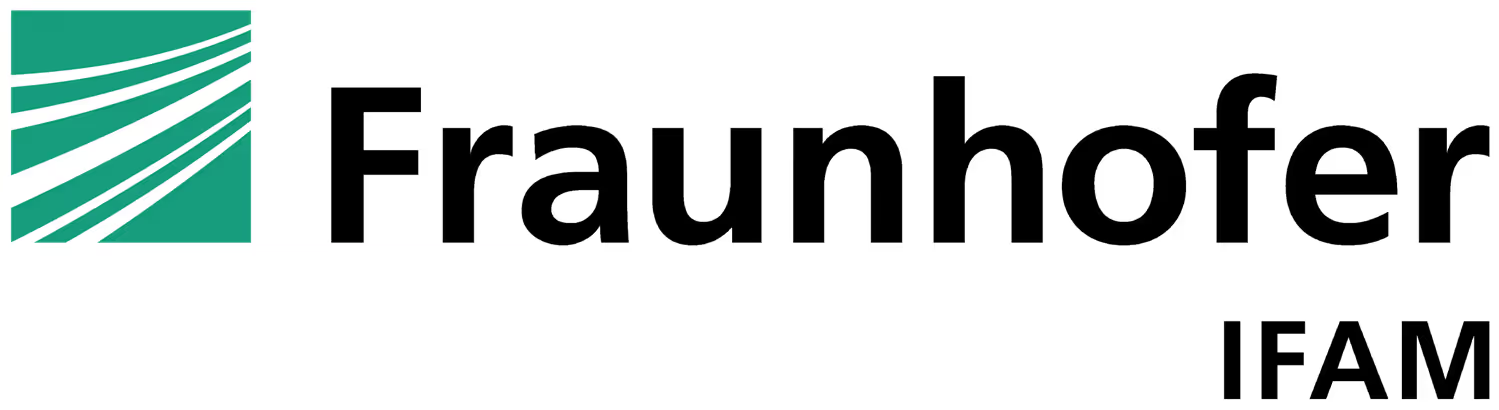
Superfaser 2
WOPOREX
PAMico
HyFiVe
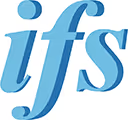
GreenFront
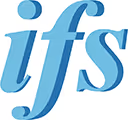
Superfaser
ReOrgAL
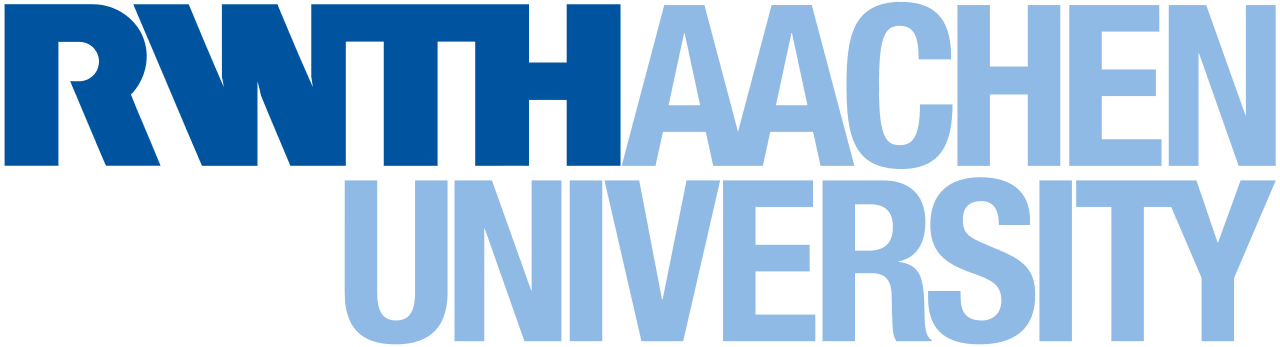
NEWWAVE
SuperCarbon
HIRSys
Permback
Esprit
HELM
Projekt FSM
PhotoRec
CLEAN-HEAT
SULFREE
DEMETO
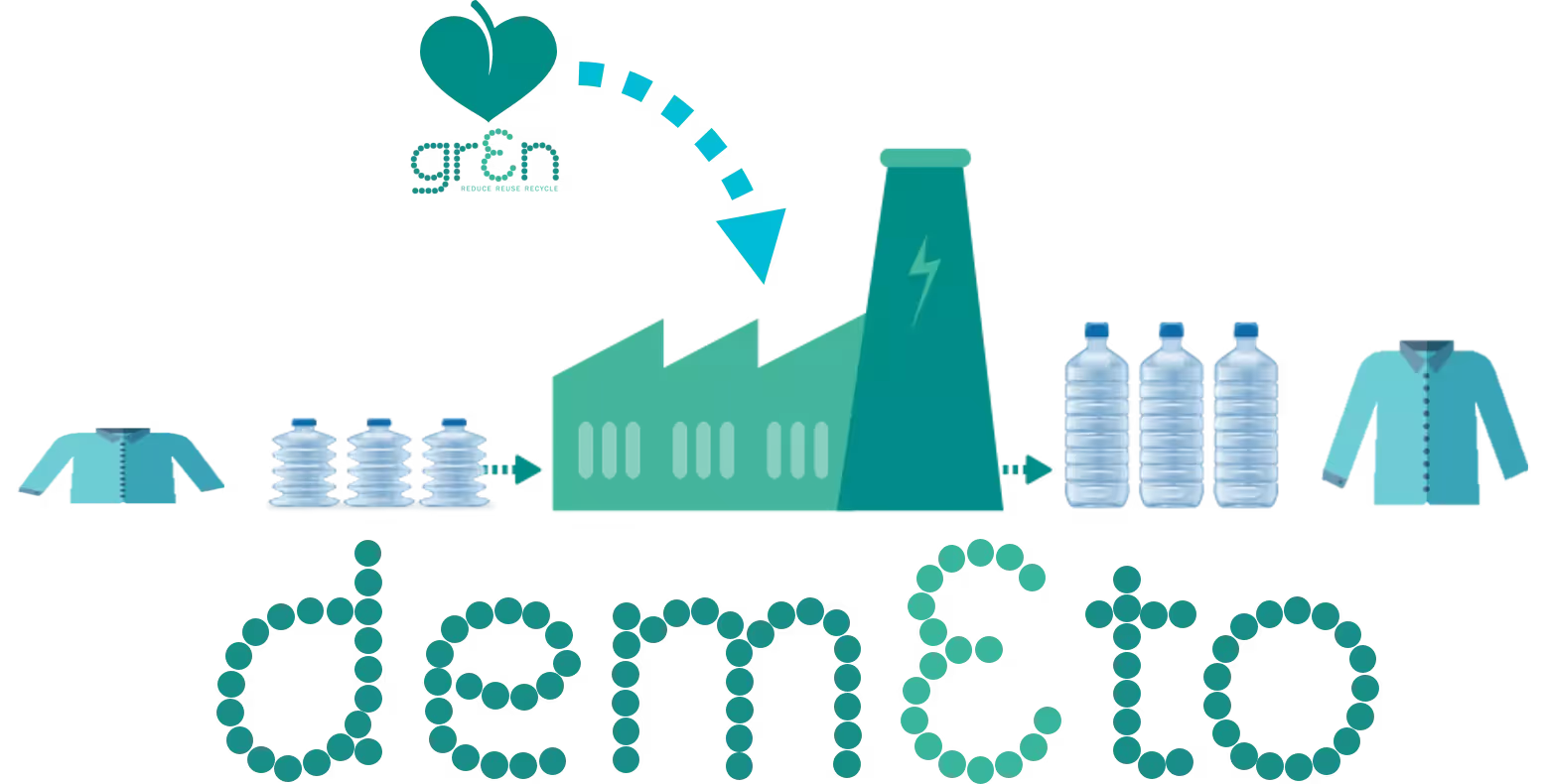
polynSPIRE
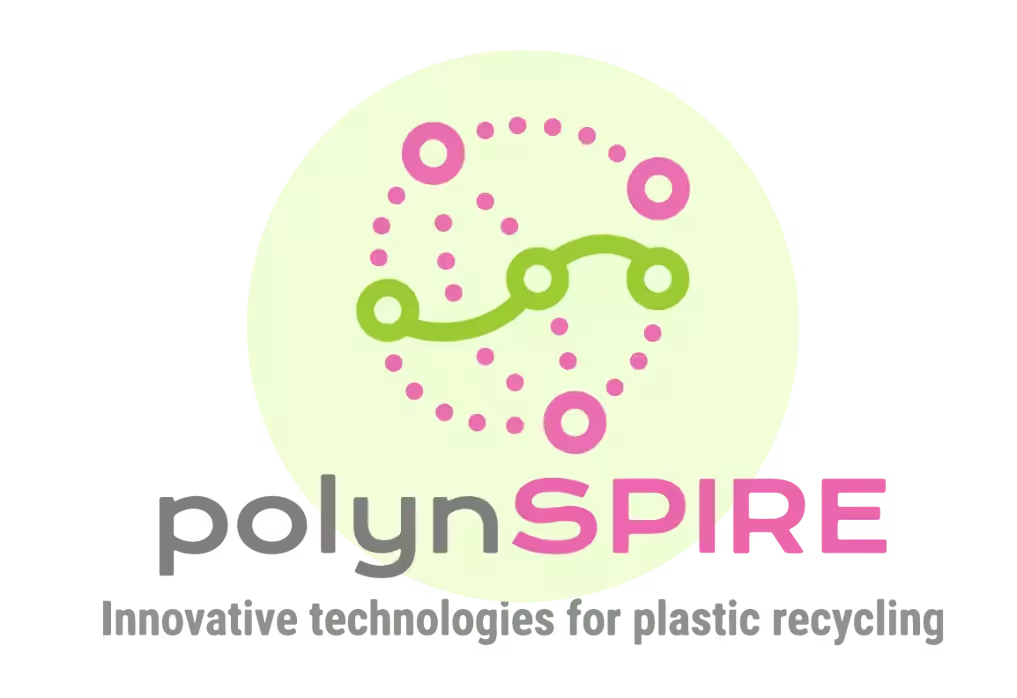
CEM-WAVE
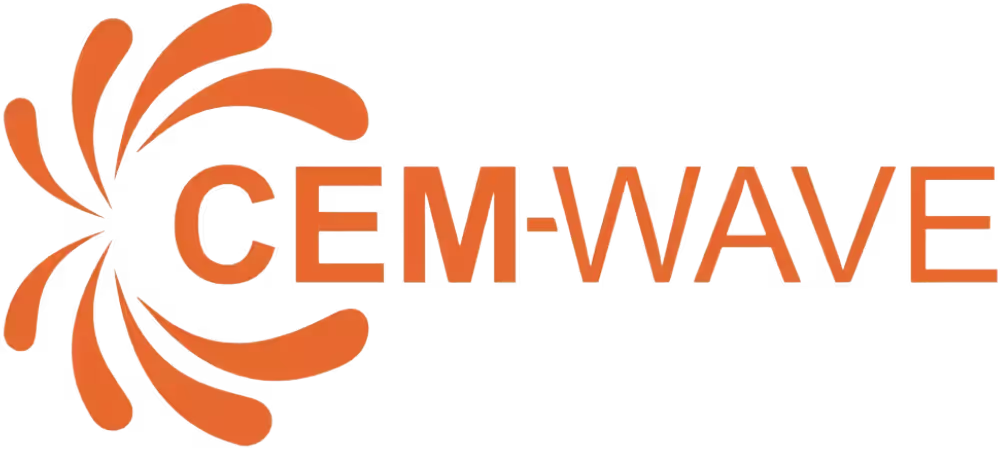
Have we convinced you?
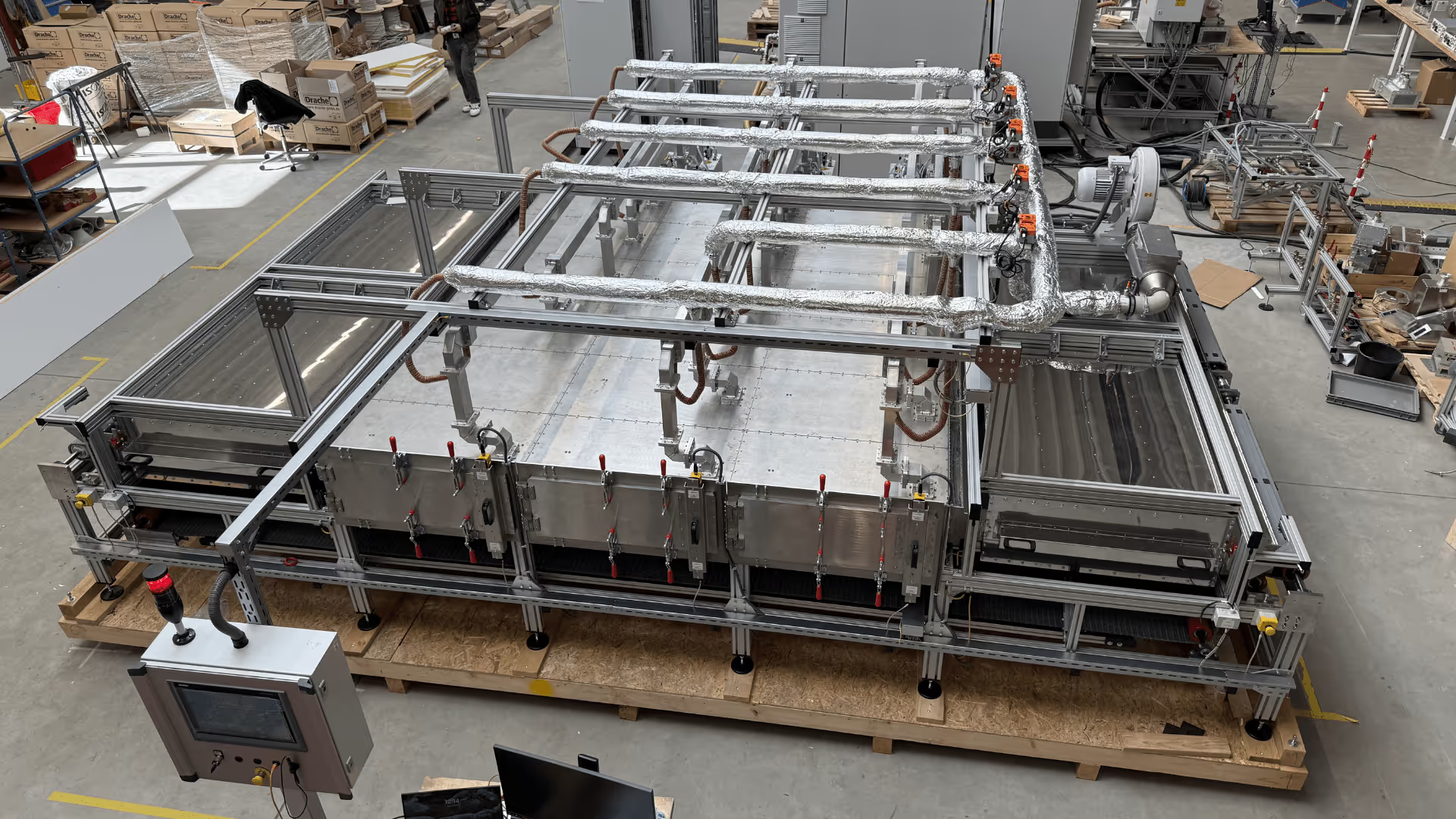