Research
Research for more efficient technologies
We are the first point of contact for the development of new, innovative methods.
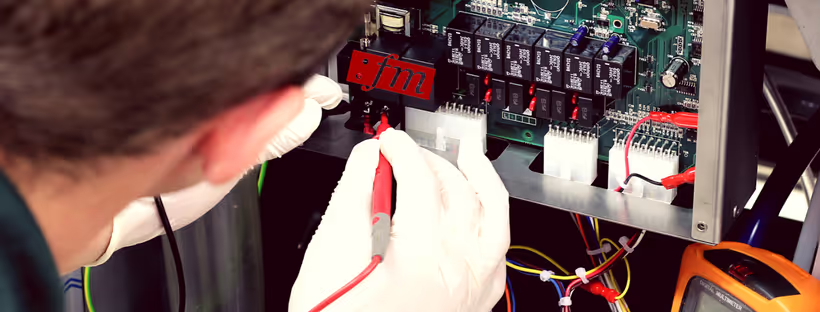
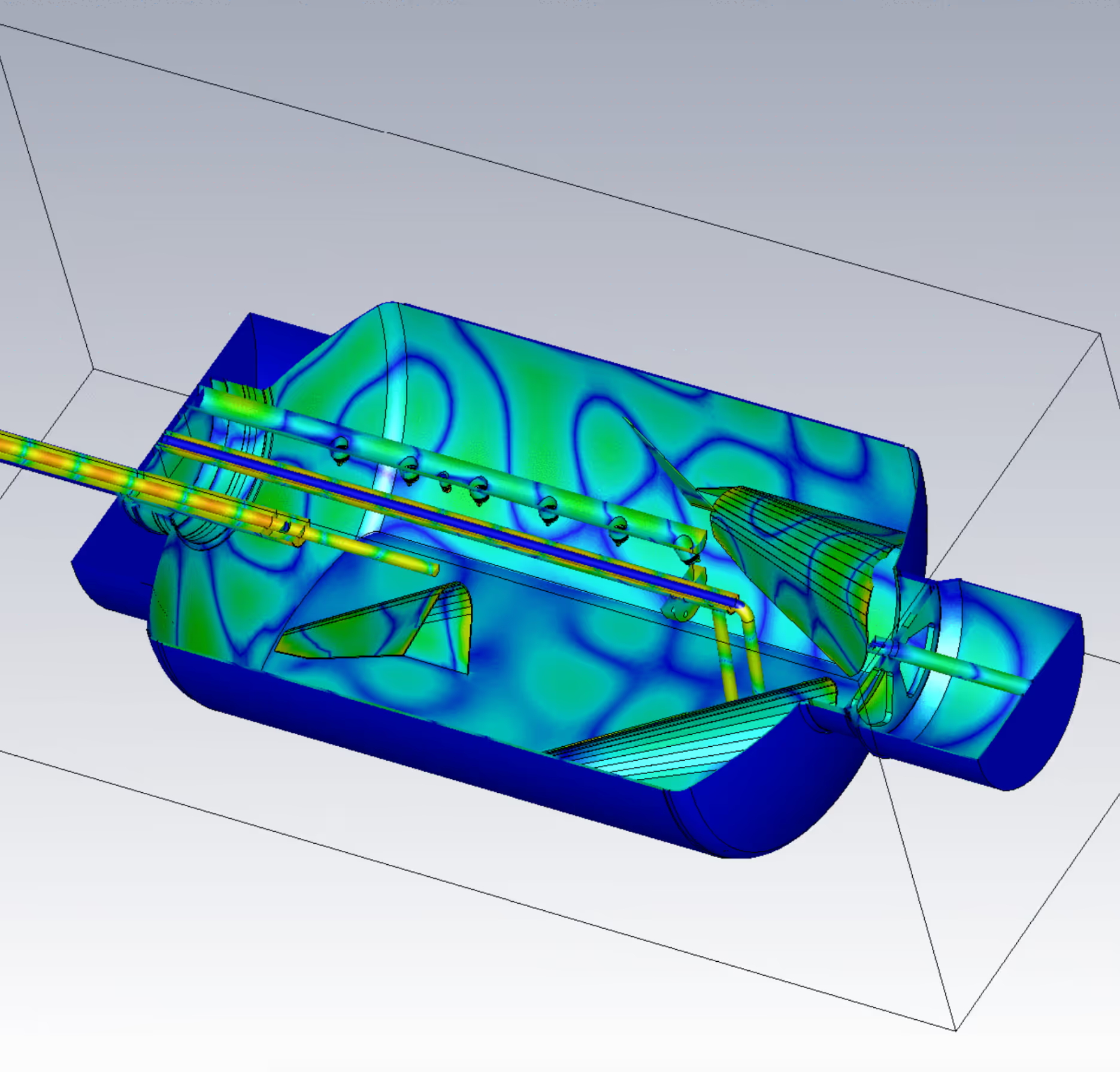
Physical simulation for predictable success in your projects
Fricke und Mallah Microwave Technology GmbH is the first port of call for the development of new, innovative processes. This is recognized in industrial and scientific research. Our services include process analysis and consulting. An important part of this is the well-founded and realistic physical simulations, which ensure that customer and research projects can be planned for success. This saves time and resources.
A selection of our research projects
Get an overview of some of the research projects we have been involved in.
CirProtech
Circular Production Polymer Technologies
2025
-
2030
BMBF

METAWAVE
High-temperature heating processes with breakthrough microwave and digital technologies for increased energy efficiency
2024
-
2028
EU
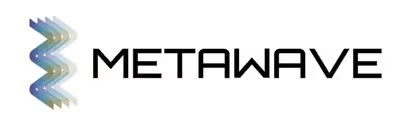
Flexby
Flexible and advanced Biofuel technology through an innovative microwave pYrolysis & hydrogen-free hydrodeoxygenation processList
2024
-
2027
EU
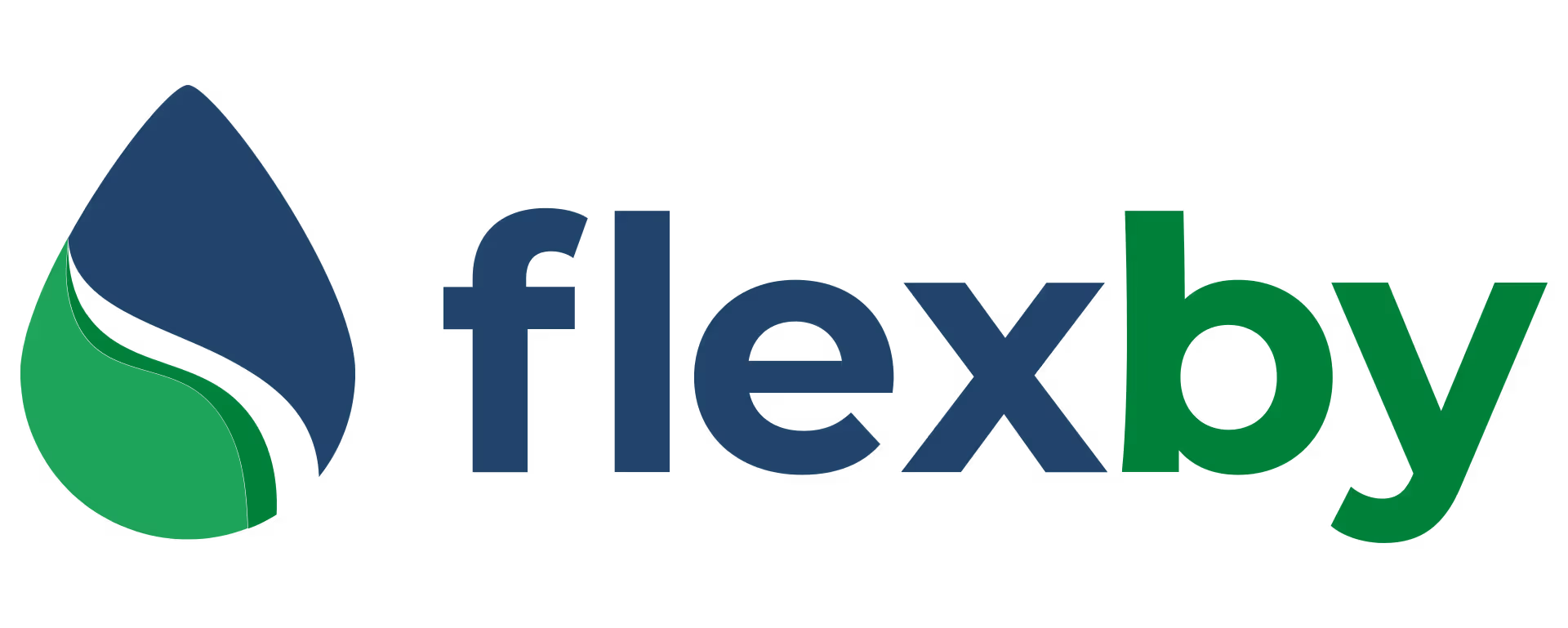
Hybrid-FIRE
Hybrid-Ofenverfahren für Hochtemperaturtechnologien zur thermischen Behandlung anorganischer Werkstoffe
2023
-
2027
BMWK
CITADEL
Substitution of fossil Combustion in Industrial high- Temperature processes by ADvanced ELectrical and plasma heating technologies
2023
-
2027
EU
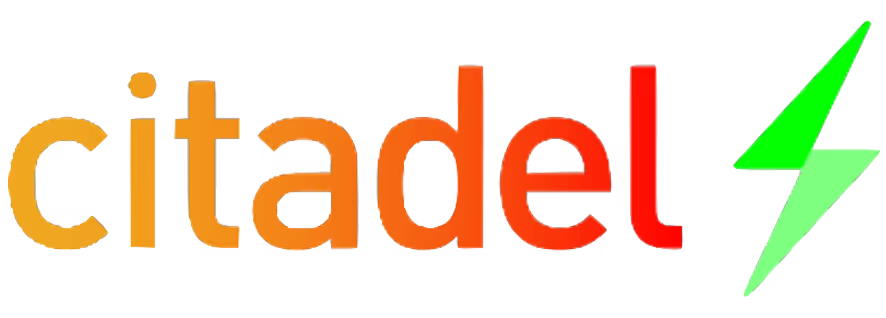
RE_SORT
Pyrolyse dickwandiger Faserverbundwerkstoffe als Schlüsselinnovation im Recyclingprozess für Rotorblätter von Windenergieanlagen
2023
-
2026
BMWK
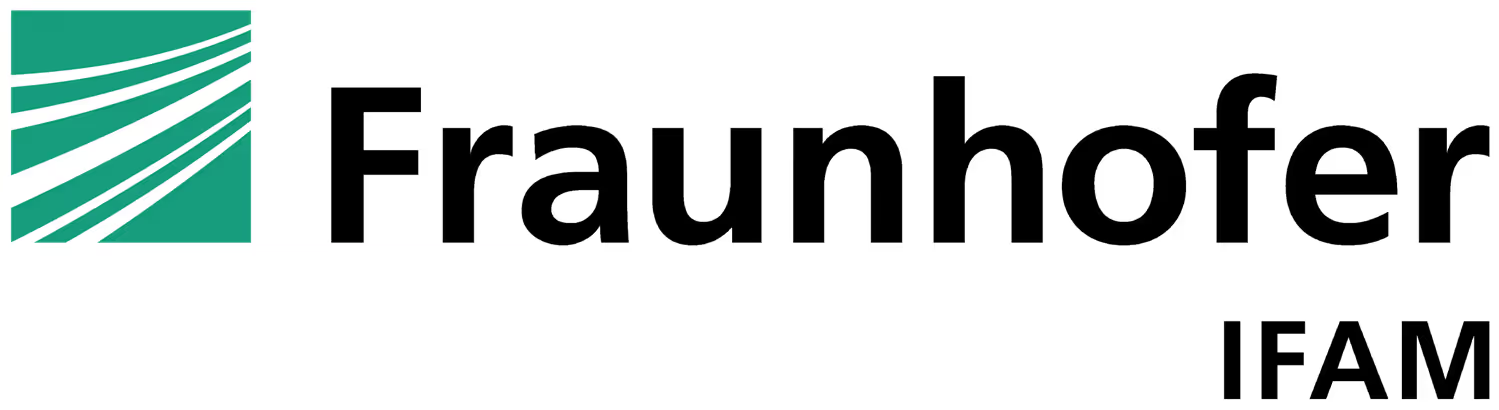
WOPOREX
Verfahren zur kontinuierlichen Produktion von Biopolymer-Monomeren durch Integration von Mikrowellenstrahlung
2022
-
2025
BMBF
HyFiVe
Großserienfähige Variantenfertigung von Kunststoff-Metall-Hybridbauteilen
2020
-
2024
BMBF
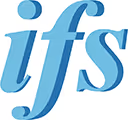
GreenFront
Nachhaltige Fassadenelemente aus Holzschaum und Textilbeton
2020
-
2023
BMBF
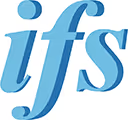
ReOrgAL
Steigerung der Energie- und Ressourceneffizienz des Recyclings organik-kontaminierter Aluminiumschrotte
2019
-
2022
BMWE
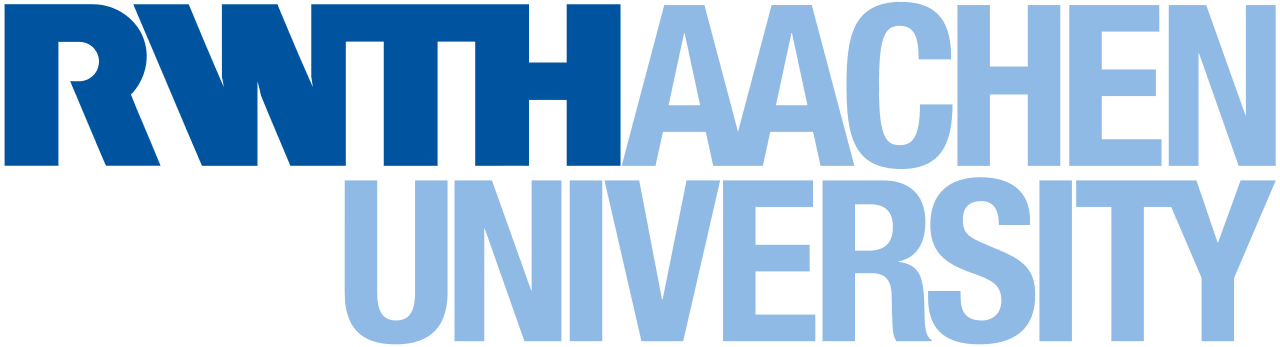
NEWWAVE
Erhitzungs- und Trocknungsverfahren für Lebensmittel mittels Mikrowellentechnologie
2018
-
2021
BMEL
SuperCarbon
Carbonfaservliese mit hierarchischer Oberflächenporosität und erhöhter Energiedichte für Superkondensatorelektroden
2017
-
2021
BMBF
HIRSys
Intelligente Hochfrequenz-Sensorsysteme für die industrielle Nahrungsmittelherstellung
2017
-
2020
BMBF
NanoWave
Mikrowellenhärtung von Isolier- und Vergussmaterialien für elektronische Baugruppen
-
PhotoRec
Rückgewinnung von seltenen strategischen Metallen aus EOL Dünnschicht-PV-Modulen
2012
-
2015
BMBF
CLEAN-HEAT
Ein hocheffizientes, intelligentes industrielles Mikrowellenheizsystem auf der Grundlage von Hochleistungs-Solid State-Technologie
-
SULFREE
Mikrowellenpyrolyse für das Recycling von Altreifen
2013
-
2016
EU
DEMETO
Modulare, skalierbare und leistungsstarke Depolymerisation mittels Mikrowellentechnologie
2017
-
2021
EU
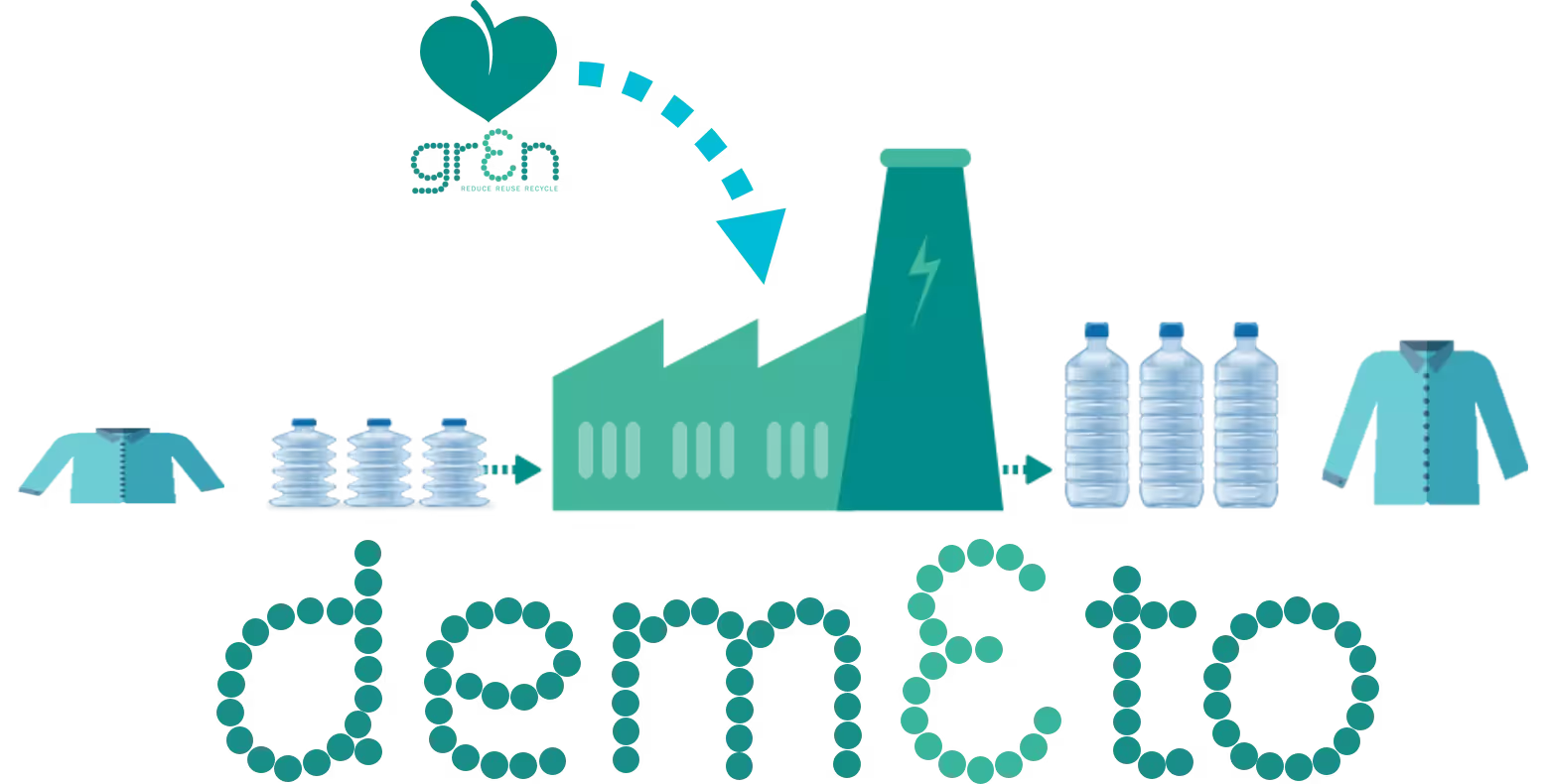
polynSPIRE
Chemisches Recycling von Kunststoffabfällen
2017
-
2021
EU
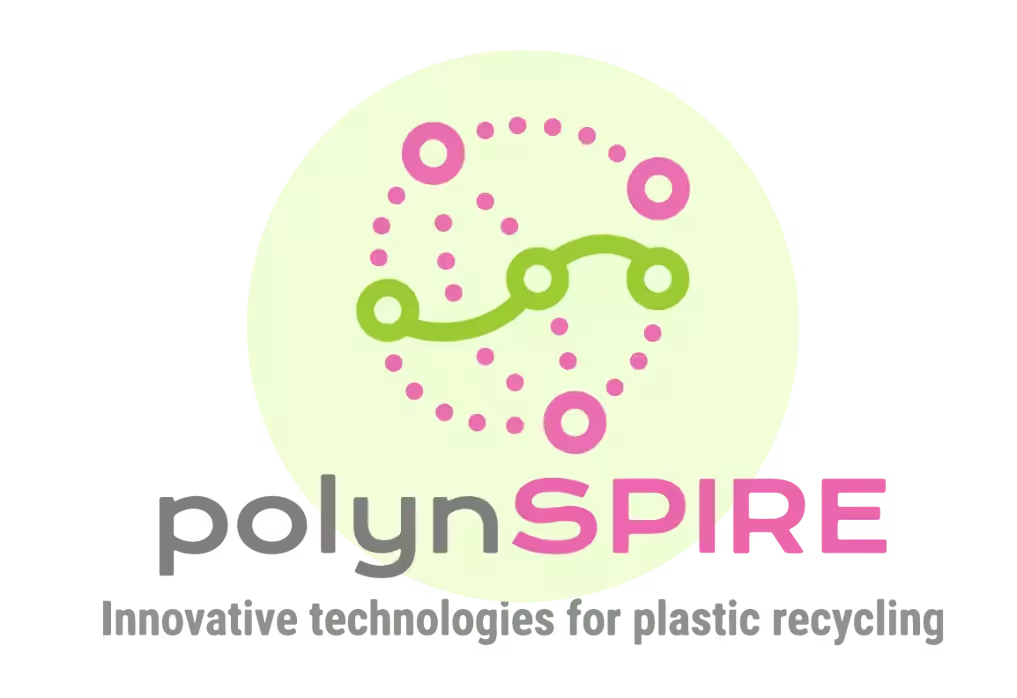
CEM-WAVE
Hochleistungswerkstoffe als Wegbereiter für eine saubere Produktion
-
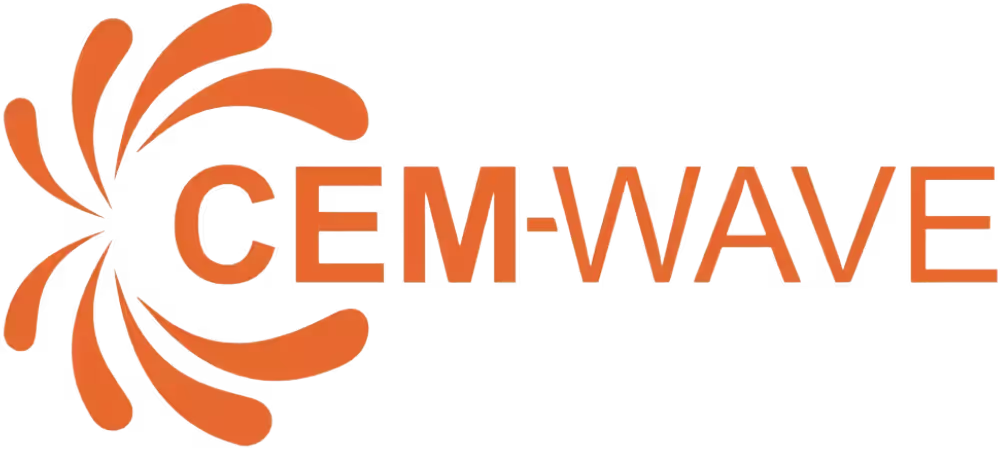
Our partners from the world of science
We work together with numerous partners from the world of science, with whom we implement innovative projects.
Our EU research partners
An overview of our EU research partners with whom we realize great projects.
Have we convinced you?
Get in touch with our team in just a few simple clicks through our website! Our experts will contact you as soon as possible.
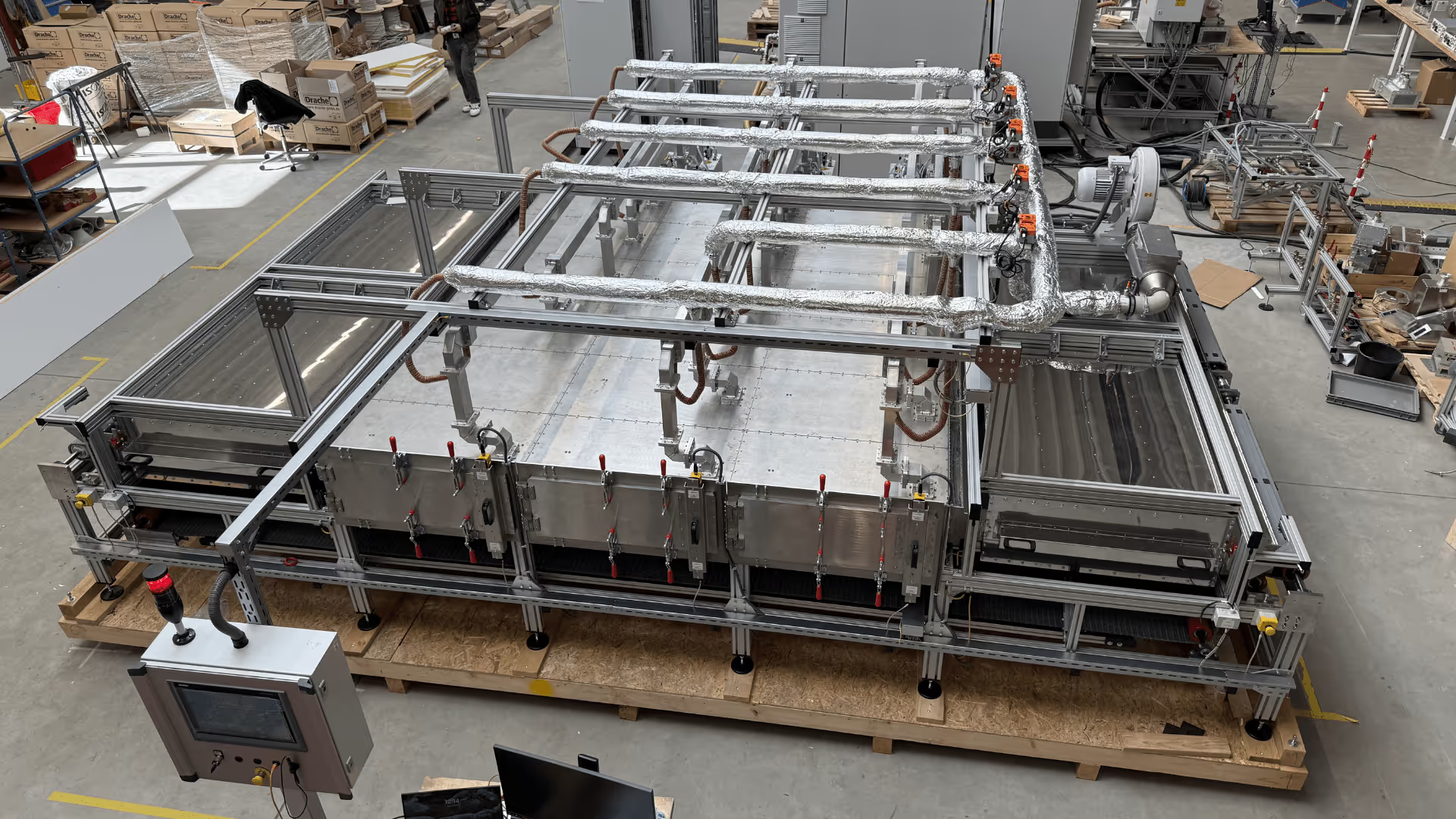