Forschung
Projekte
Wissenschaftliche Forschung für effizientere Technologien
Wir sind Ihr Ansprechpartner für die Entwicklung neuer und innovativer Methoden.
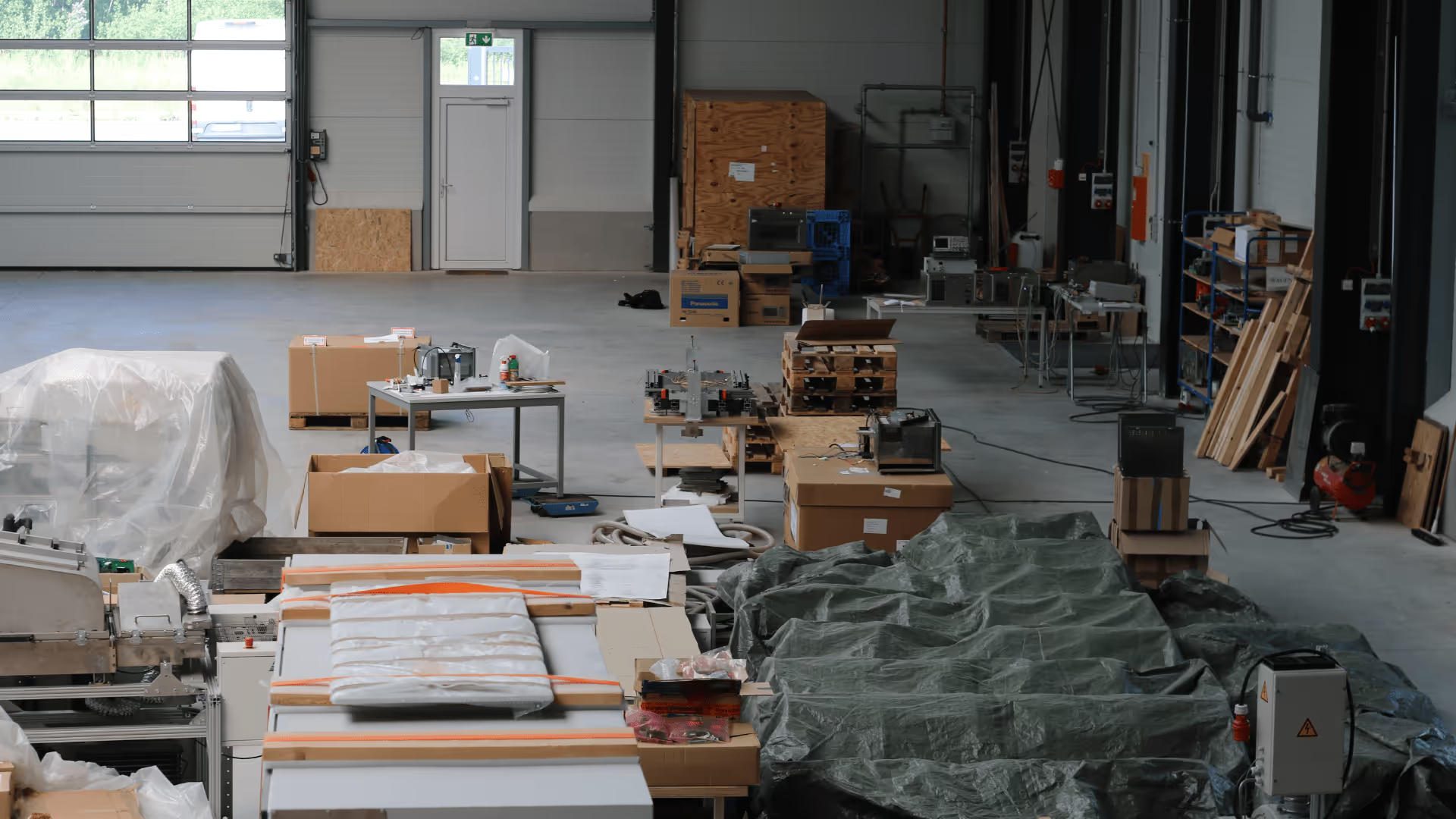
Wissenschaftliche Forschung für effizientere Technologien
Die Fricke und Mallah Microwave Technology GmbH ist die erste Anlaufstelle für die Entwicklung neuer innovativer Methoden. Dies wird auch in der wissenschaftlichen Forschung anerkannt. Unsere erfahrenen Physiker und Hochfrequenzingenieure sind absolute Experten auf ihrem Gebiet, was in zahlreichen industriellen und wissenschaftlichen Forschungsprojekten bestätigt wurde.
- Kunststoff-Recycling
- Verbesserung der Backprozesse
- Organobleche auf Kohlefaserbasis
- Kohlefaser-Fasern
- Gefriertrocknung
- Pyrolyseverfahren
- Streckblasverfahren
- Umweltfreundlich und energieeffizient
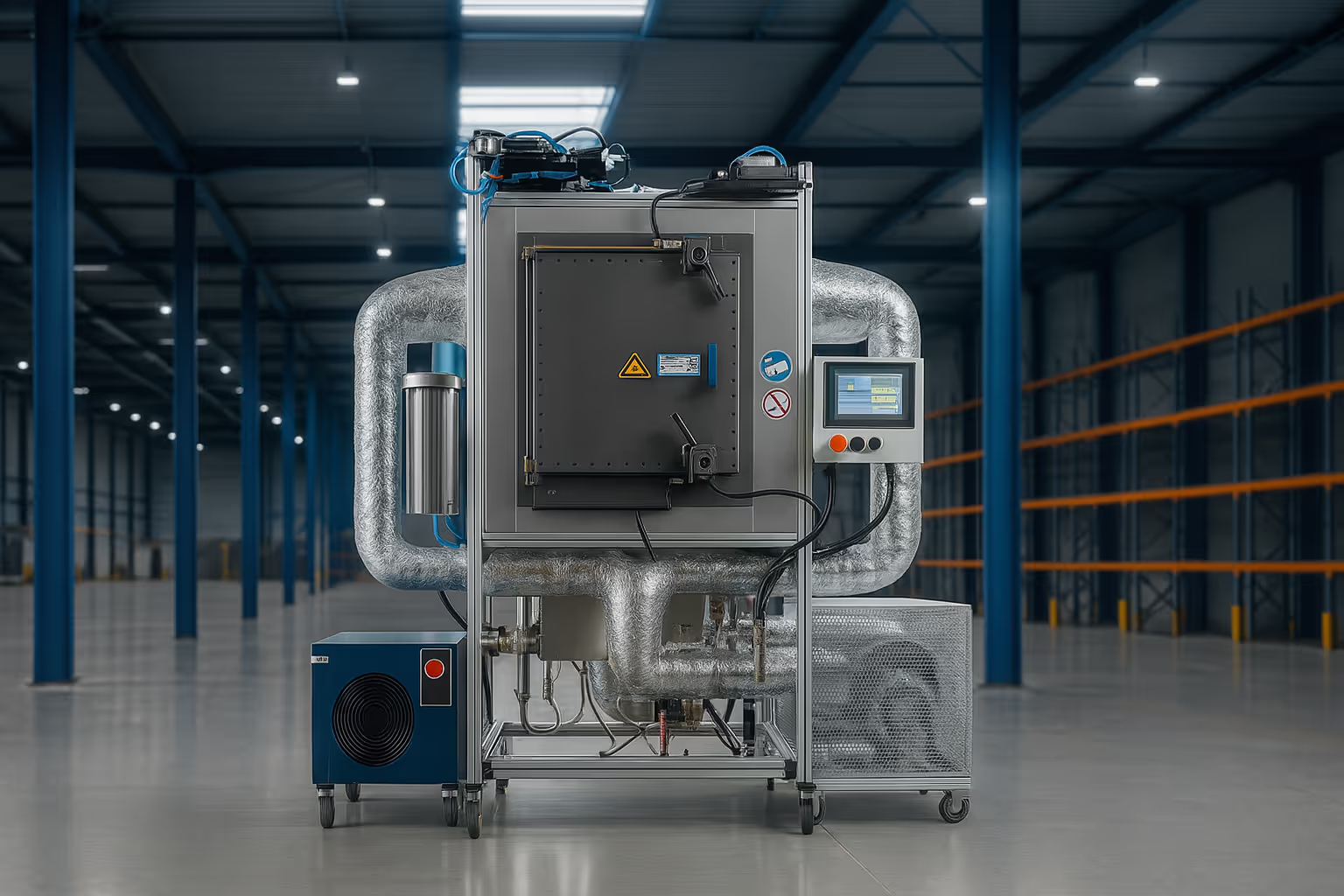
CirProtech
Circular Production Polymer Technologies
2025
-
2030
BMBF

METAWAVE
High-temperature heating processes with breakthrough microwave and digital technologies for increased energy efficiency
2024
-
2028
EU
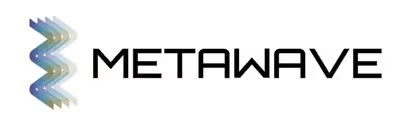
MIND
Mikrowellenprozesstechnik für die silikatkeramische Industrie unter Berücksichtigung prozessrelevanter Eigenschaften
2024
-
2027
BMBF
Flexby
Flexible and advanced Biofuel technology through an innovative microwave pYrolysis & hydrogen-free hydrodeoxygenation processList
2024
-
2027
EU
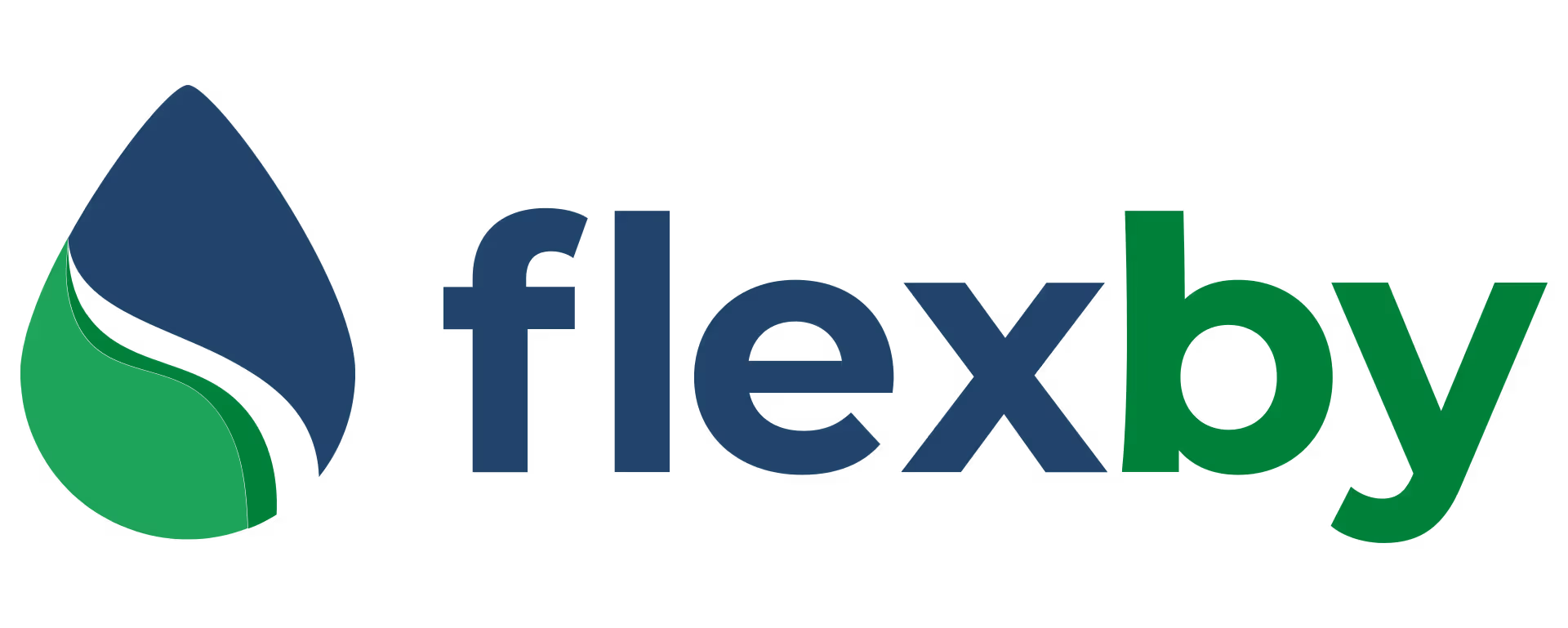
Hybrid-FIRE
Hybrid-Ofenverfahren für Hochtemperaturtechnologien zur thermischen Behandlung anorganischer Werkstoffe
2023
-
2027
BMWK
CITADEL
Substitution of fossil Combustion in Industrial high- Temperature processes by ADvanced ELectrical and plasma heating technologies
2023
-
2027
EU
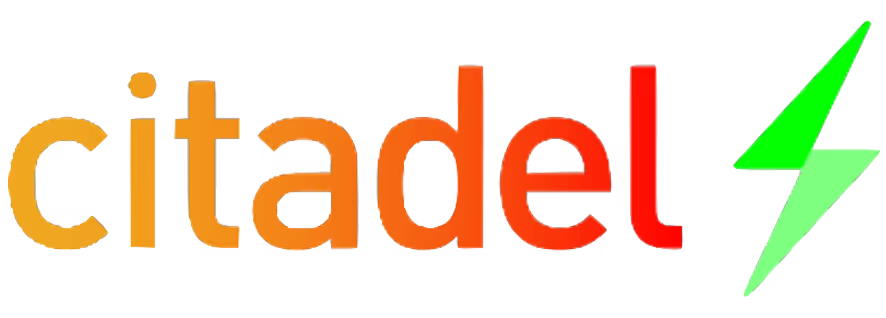
DevEI
Entwicklung eines halbleiterbasierten Mikrowellenverfahrens zur Devulkanisation von schwefelvernetzenden Elastomeren
2024
-
2026
BMBF
RE_SORT
Pyrolyse dickwandiger Faserverbundwerkstoffe als Schlüsselinnovation im Recyclingprozess für Rotorblätter von Windenergieanlagen
2023
-
2026
BMWK
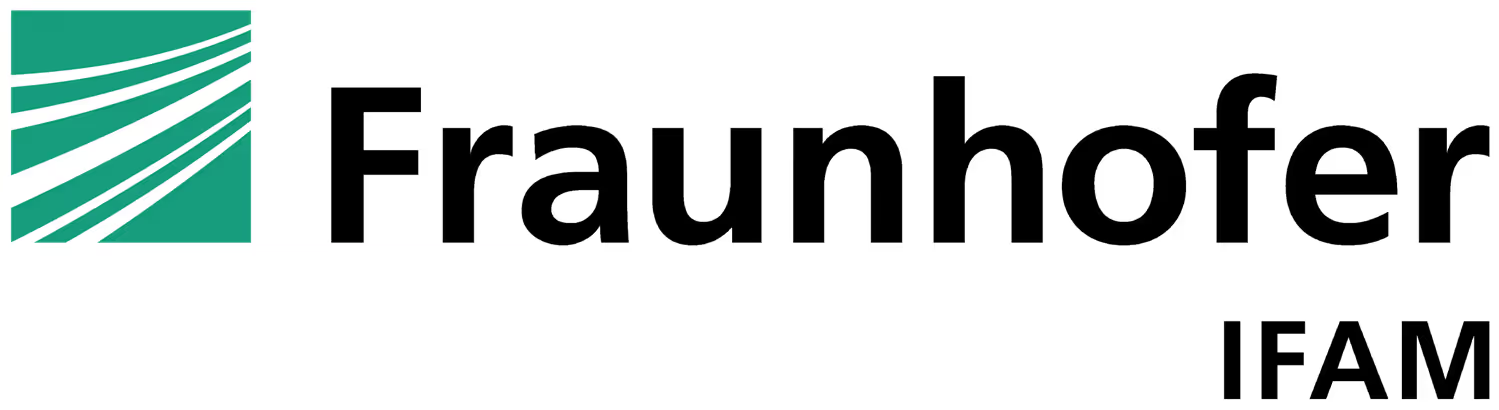
Superfaser 2
Umweltschonende Umwandlungsprozesse mit reduziertem Energieeintrag durch GHz-Plasma in der Carbonfaserherstellung – Teil 2
2023
-
2025
DBU
WOPOREX
Verfahren zur kontinuierlichen Produktion von Biopolymer-Monomeren durch Integration von Mikrowellenstrahlung
2022
-
2025
BMBF
PAMico
Phased Array Antenna for Microwave based Weed Control
2022
-
2025
BMWK
HyFiVe
Großserienfähige Variantenfertigung von Kunststoff-Metall-Hybridbauteilen
2020
-
2024
BMBF
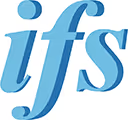
GreenFront
Nachhaltige Fassadenelemente aus Holzschaum und Textilbeton
2020
-
2023
BMBF
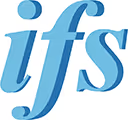
Superfaser
Umweltschonendere Spinnprozesse und reduzierter Energieeintrag durch GHz-Plasma in der Carbonfaserherstellung
2020
-
2022
DBU
ReOrgAL
Steigerung der Energie- und Ressourceneffizienz des Recyclings organik-kontaminierter Aluminiumschrotte
2019
-
2022
BMWE
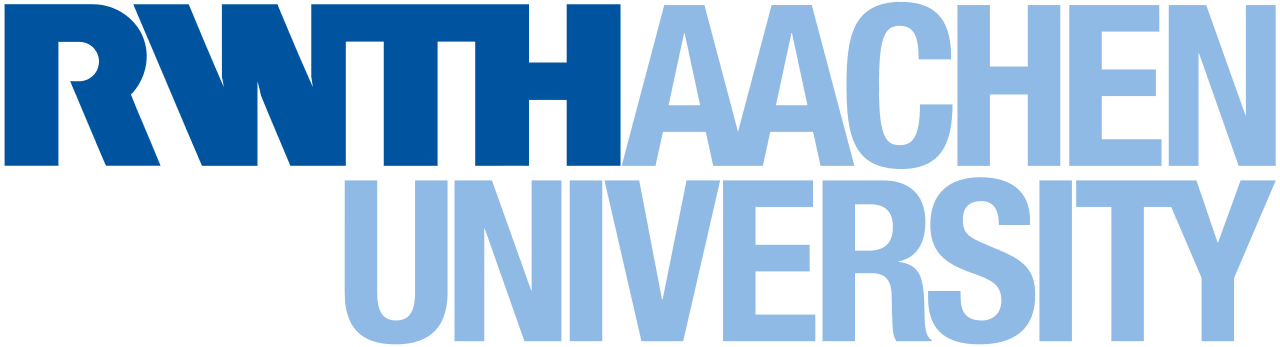
NEWWAVE
Erhitzungs- und Trocknungsverfahren für Lebensmittel mittels Mikrowellentechnologie
2018
-
2021
BMEL
SuperCarbon
Carbonfaservliese mit hierarchischer Oberflächenporosität und erhöhter Energiedichte für Superkondensatorelektroden
2017
-
2021
BMBF
HIRSys
Intelligente Hochfrequenz-Sensorsysteme für die industrielle Nahrungsmittelherstellung
2017
-
2020
BMBF
Permback
Thermo-Hybrid-Mikrowellendurchlaufofensystem mittels Halbleiter- Mikrowellentechnologie für die Backwarenherstellung.
2017
-
2019
BMWi
HELM
Elektromagnetische Hochfrequenztechnologien für die fortschrittliche Verarbeitung von Verbundwerkstoffen mit Keramikmatrix und Graphitexpansion
-
Projekt FSM
Desinfektion von Fäkalien durch Mikrowellen
-
PhotoRec
Rückgewinnung von seltenen strategischen Metallen aus EOL Dünnschicht-PV-Modulen
2012
-
2015
BMBF
CLEAN-HEAT
Ein hocheffizientes, intelligentes industrielles Mikrowellenheizsystem auf der Grundlage von Hochleistungs-Solid State-Technologie
-
SULFREE
Mikrowellenpyrolyse für das Recycling von Altreifen
2013
-
2016
EU
DEMETO
Modulare, skalierbare und leistungsstarke Depolymerisation mittels Mikrowellentechnologie
2017
-
2021
EU
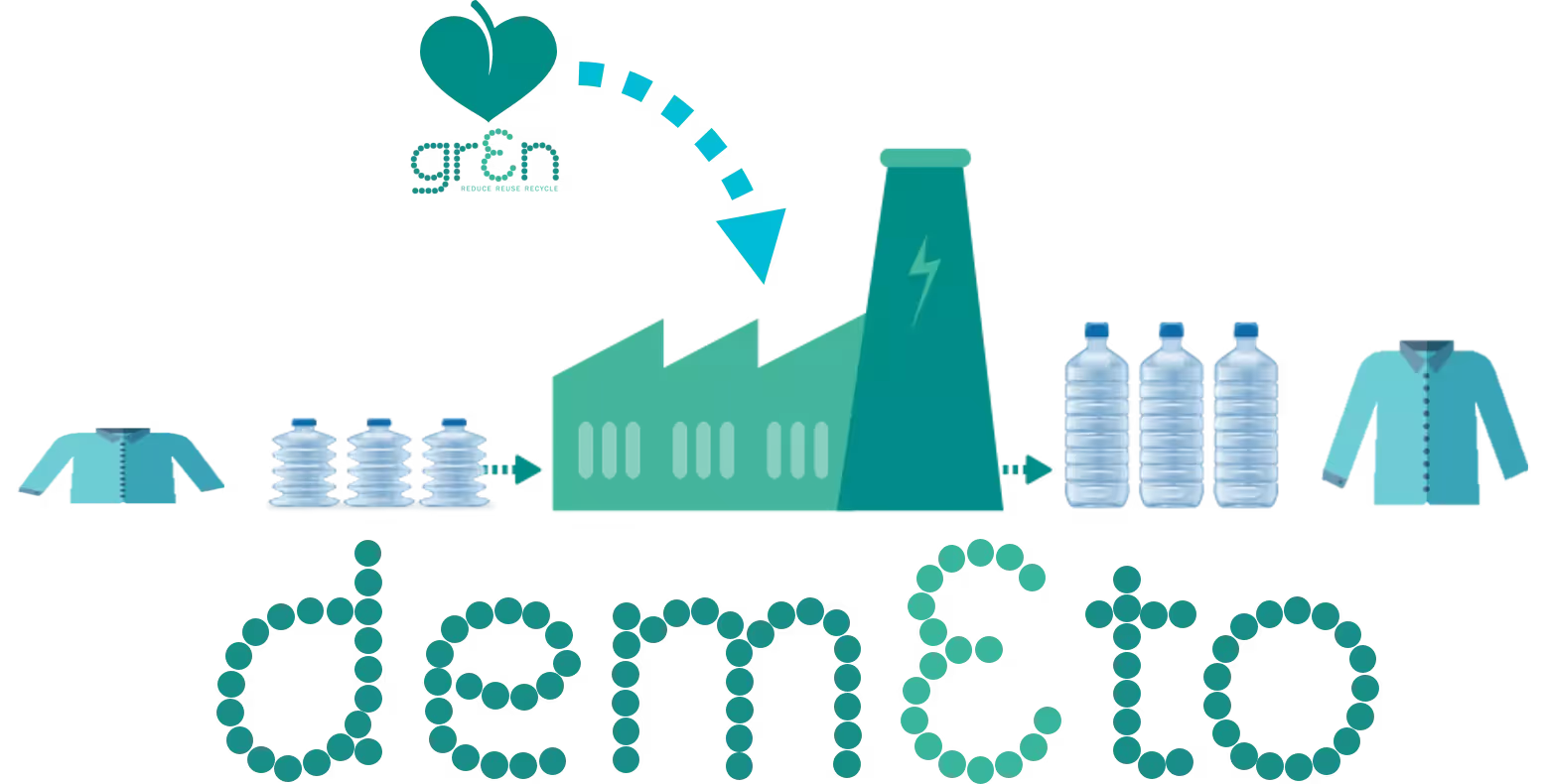
polynSPIRE
Chemisches Recycling von Kunststoffabfällen
2017
-
2021
EU
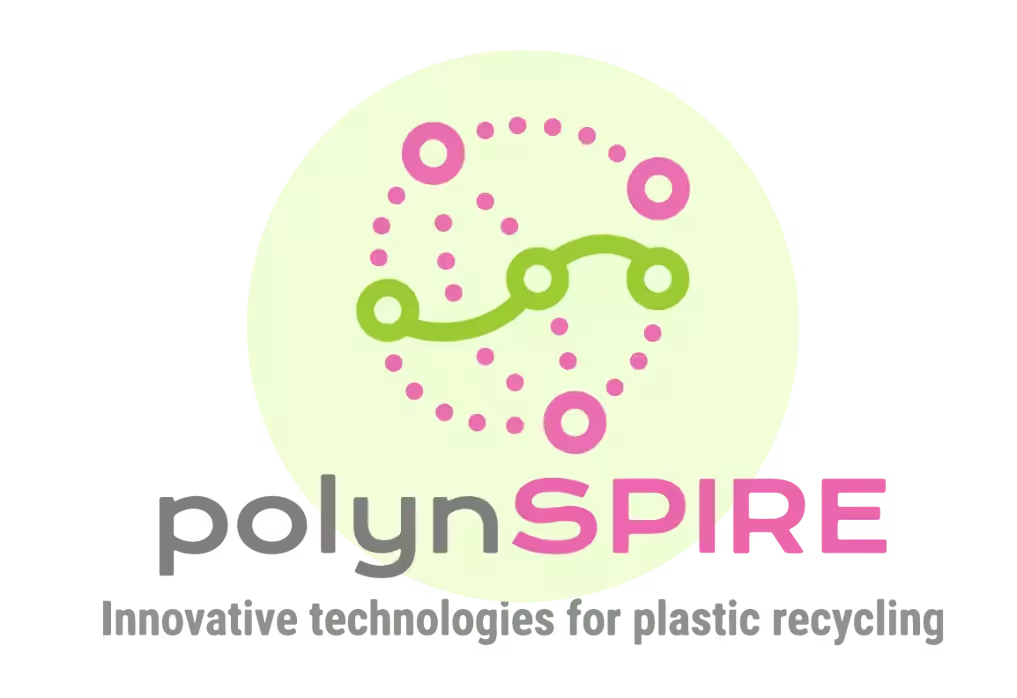
Haben wir Sie überzeugt?
Nehmen Sie mit nur wenigen Klicks über unsere Website Kontakt mit unserem Team auf! Unsere Experten werden Sie so schnell wie möglich kontaktieren.
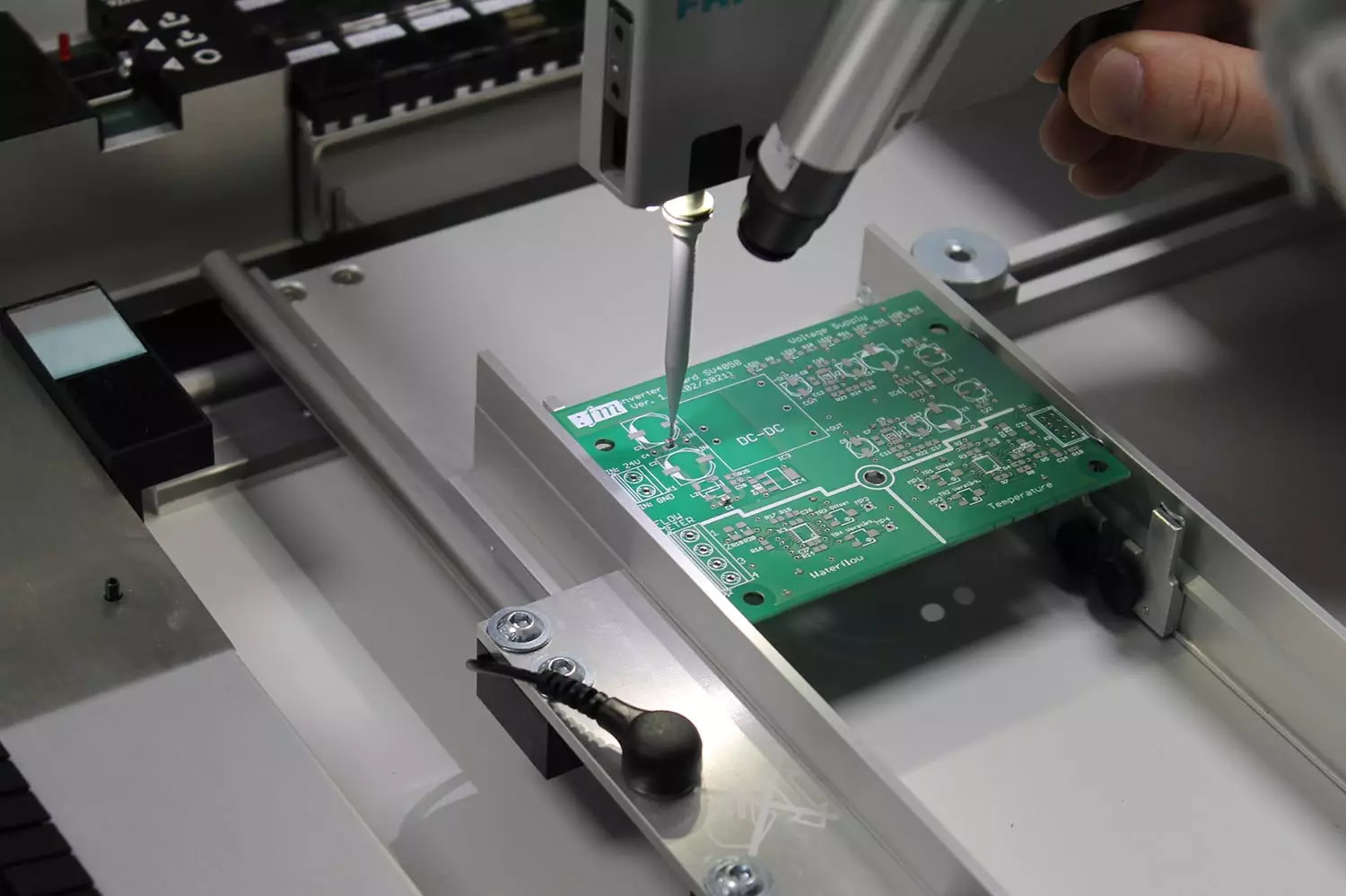