Efficient microwave chamber ovens
Our range of high-quality chamber ovens for drying and heating products
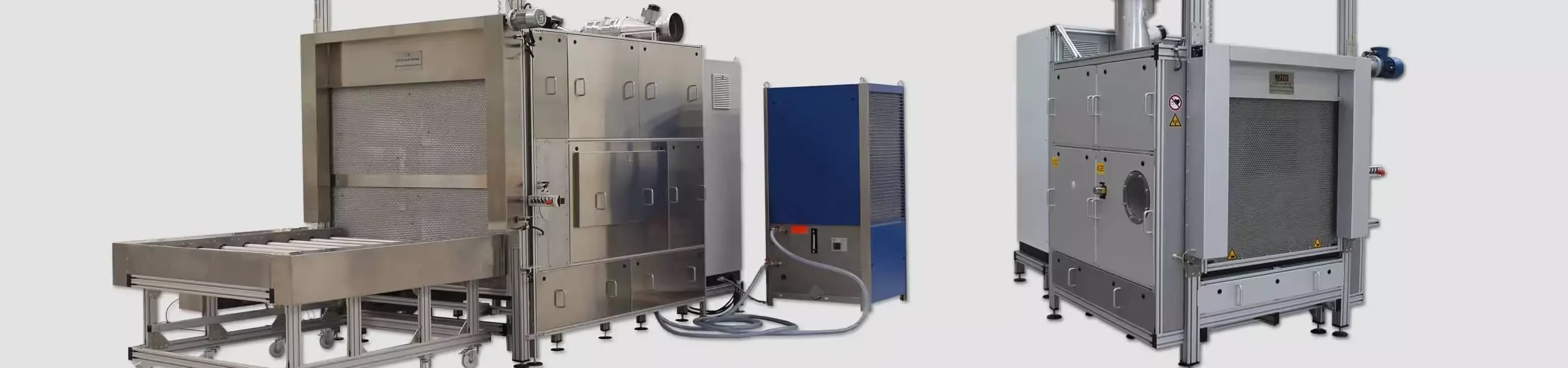
Highly innovative, future-oriented microwave chamber ovens
Our customized microwave chamber ovens have been used successfully for years in research and industry to dry, heat and sinter products under various atmospheres (e.g. vacuum, overpressure, inert gas). They can also be designed as hybrid systems in which microwave generators are combined with conventional heating methods such as hot air, resistance heating, IR, heat pumps or microwave plasma burners. This allows customized temperature-time profiles to be implemented for optimum product quality and energy efficiency. Thanks to electromagnetic simulations, the microwave coupling points and chamber dimensions are designed for high field homogeneity, which enables gentle drying, short times and high-quality results. Oscillating supports or turntables are often integrated for even heat distribution, and condensation is prevented by technical measures.
Drastic time savings
The acquisition drastically shortens prototype development times and speeds up the time to series production.
Customized options
In addition to prototypes, special customer requirements can be quickly implemented in small series.
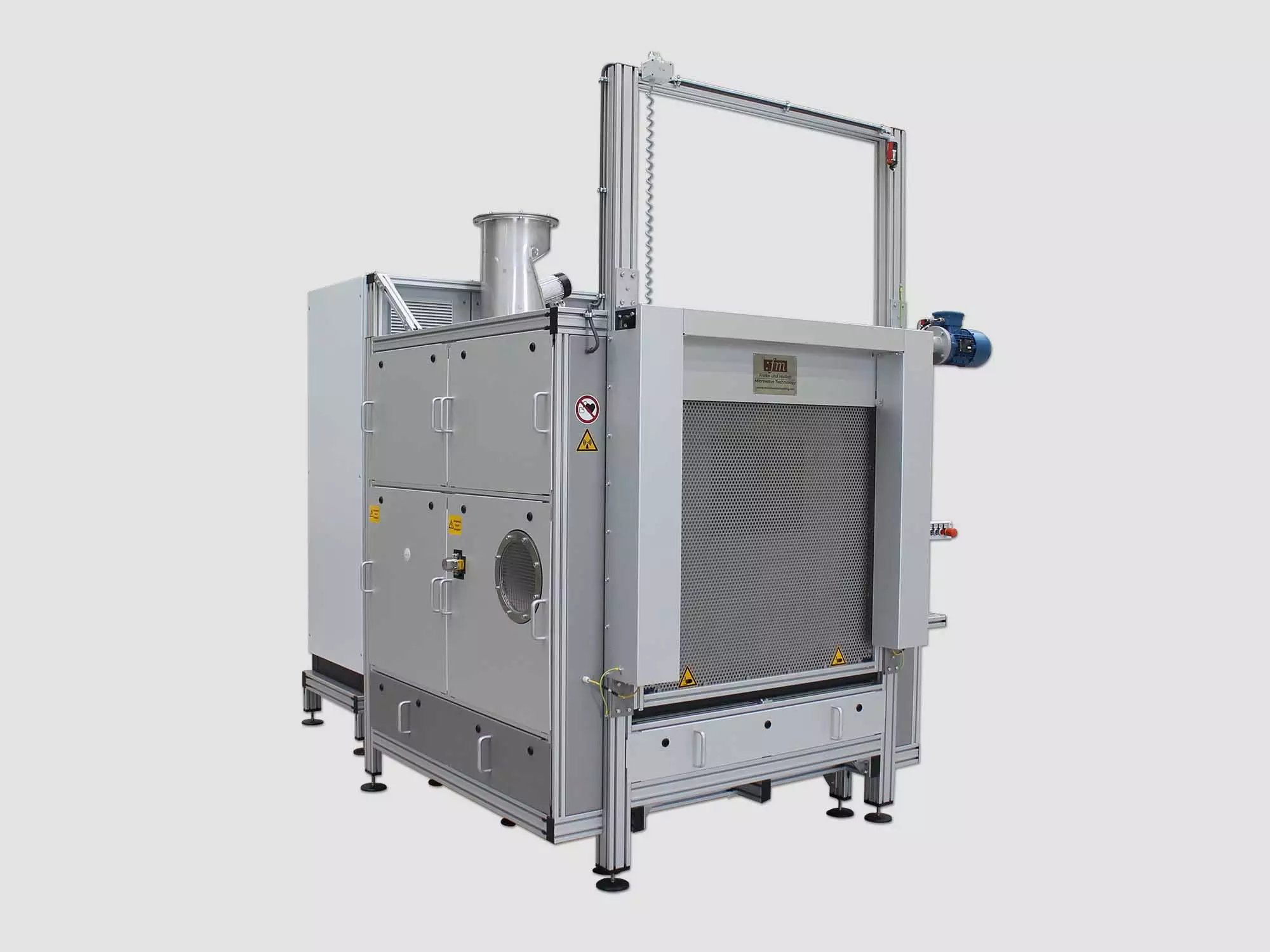
Product examples
Have we convinced you?
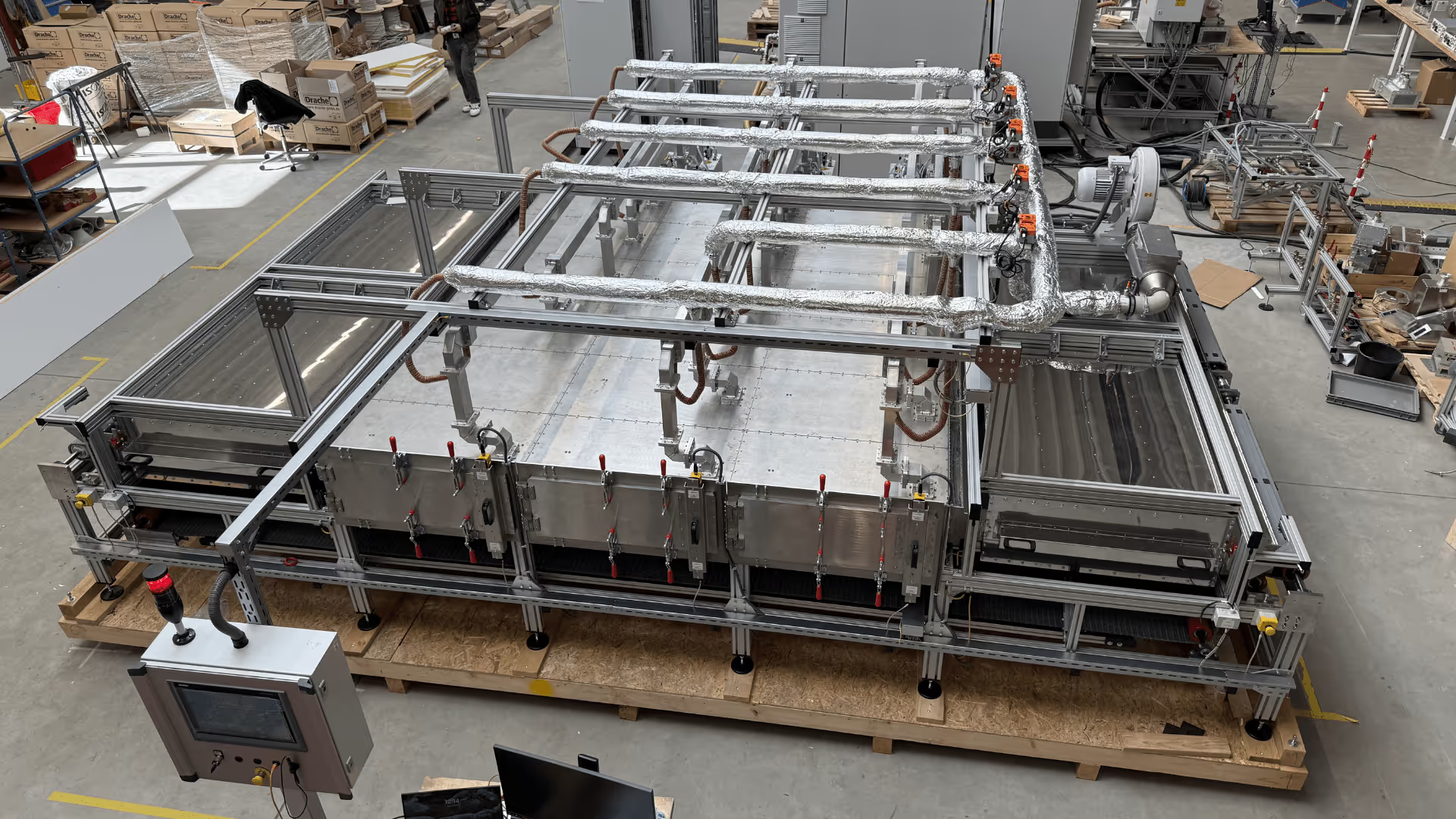